Ready for Industry 4.0 with TR-Electronic
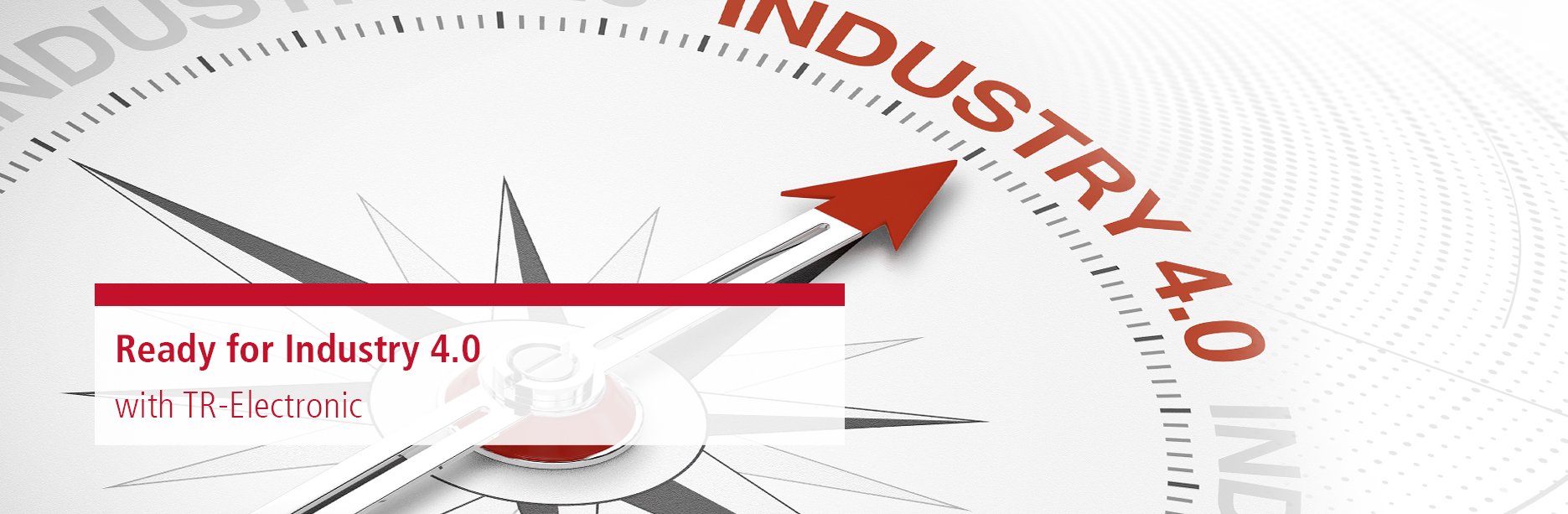
Comprehensive networking and open communication between systems are the driving force for Industry 4.0. The increasing individualization of products and the implementation of additional functions in production systems, coupled with the demand for reasonable prices, call for intelligent and adaptive production systems which can communicate with each other. Direct exchange of recipe and process control data, dynamic adaptation of production processes and material flow as well as product-related documentation ensure high flexibility, enabling the fulfillment of diverse user requirements coupled with efficient production.
- TR sensors as a source for “Big-Data” condition monitoring
- Process and condition data for processing in control systems
- Motion data (rotary speed ranges, number of turns
- Communication data and failures
- Power supply data and failures
- Environmental conditions (sensor core temperature…)
- Uses asynchronous data channels in fieldbusses and industrial Ethernet.
Machine and system manufacturers seek to analyze the condition of the system using a wide variety of acquired process data and so avoid undesirable conditions such as faulty production or system shutdowns. To this end machine and system controllers collect a great deal of data, which at first glance is not crucial for the actual process, and analyze it using "Big Data" methods. Generally, this has little to do with the condition of the rotary encoder itself: Install, connect, forget. What is much more interesting is the condition of wear-prone components.
An example:
For a positioning process, only the position reached is actually interesting – as the feedback variable, this is the central component of the position control. For the service life of installed drive components (bearings, shafts, motors) however, other interesting factors are how often, with which axis speeds and with which torque the positioning process has been performed. Information about frequency and speed is provided by a rotary encoder, while the torque is determined by the converter from the current values. If a higher-level system collates this data, a comprehensive picture of the system condition results. It could also be interesting to record the frequency of momentary failures in communication with individual sensors, in order to predict a developing cable break in a cable carrier, before the system module concerned fails unexpectedly.
The possibilities are almost unlimited. The interaction of sensors, control level, data storage and evaluation provides users and designers of machines and systems with a comprehensive picture.
Rotary and linear encoders from TR-Electronic, particularly if designed with field bus and Industrial Ethernet interfaces, internally record far more data than the position and speed values that are primarily crucial for the process. Depending on interface and product family this can include information about the quality of the power supply, the status of the network connection, speed ranges over time…
Designers and installers, or often only the operators, can record and statistically evaluate the entirety of the data of different systems and machines in a targeted manner. In the current sensor families TR-Electronic offers a wide range of characteristic data which can be used for an assessment of the overall condition, and makes it available via standardized communication channels in Industrial Ethernet or in the traditional field bus.
The extended sensor data in the rotary and linear encoders from TR-Electronic can, if meaningfully merged and evaluated with other data, provide valuable information about machines and facilities.